In recent years, with the continuous development of the industrial field and the improvement of product quality
requirements, nondestructive testing technology plays a crucial role in the field of quality control. Among them,
Acoustic Emission Testing (AT), as an advanced non-destructive testing method, has been widely used in industry.
In this paper, we will introduce the principle and application of Acoustic Emission Testing, and discuss its advantages
and disadvantages in practical engineering.
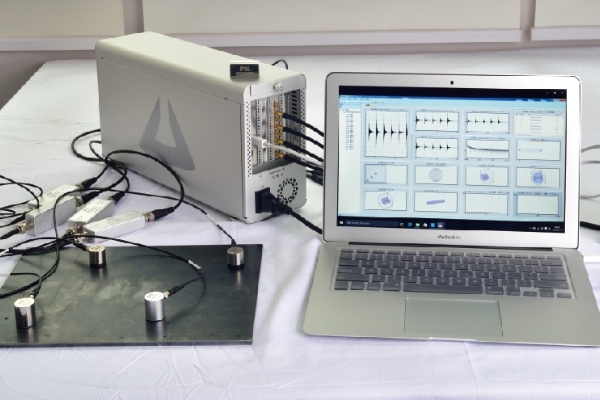
Main body
1. Principle of acoustic detection
Acoustic Emission Inspection utilizes acoustic signals generated when an object is subjected to external stress
or load to determine its structural integrity and the presence of defects. This is based on the phenomenon of
a small release of energy, known as Acoustic Emission, when a material is subjected to a force. An Acoustic
Emission Inspection system typically consists of a transducer, an amplifier and a data acquisition unit. The
transducer converts the received acoustic signals into electrical signals, which are transmitted to an amplifier
for amplification and processing. The data acquisition unit is responsible for recording and analyzing the
acoustic signals, as well as locating and evaluating defects.
2. Acousto-Electric Inspection Applications
Acoustic emission testing is widely used in non-destructive evaluation and quality control of metal materials,
concrete and other structural materials. Specific application areas mainly include the
following aspects:
Structural health monitoring: Acoustic emission testing can be used for real-time monitoring of buildings,
bridges and other engineering structures to detect potential defects or damages at an early stage in order
to avoid accidents.
Material fatigue assessment: acoustic emission detection can be used to monitor the fatigue life of metal
materials under continuous cyclic loading, and timely detection of fatigue cracks and damage expansion.
Pressure vessel safety assessment: acoustic emission testing can be used to assess the safety of the use of
pressure vessels and other equipment, timely detection of pressure leaks, cracks and other defects.
Failure diagnosis and prevention: acoustic emission detection can also be used for fault diagnosis, by analyzing
the spectrum and characteristics of the acoustic emission signal, to determine which parts of the system is
abnormal, in order to take corrective measures.
3. Advantages and disadvantages of acoustic emission testing
As a non-destructive testing method, acoustic emission testing has the following advantages:
Non-invasive: acoustic emission detection does not require destructive testing of the object under test, and is
capable of detecting large structures or objects with complex shapes.
Real-time: acoustic emission testing can monitor the defects or damage of the structure in real time, early
detection of problems and improve safety.
High sensitivity: acoustic emission detection is sensitive to small defect signals and can detect potential defects
that are difficult to detect by conventional methods.
However, there are some limitations and drawbacks of acoustic emission detection:
Complex signal interpretation: Due to the diversity and complexity of the characteristics of the acoustic signal,
the interpretation of the acoustic signal requires extensive experience and expertise.
Limited localization accuracy: The localization accuracy of acoustic emission detection for defects is relatively
low, and usually needs to be combined with other methods for further confirmation.
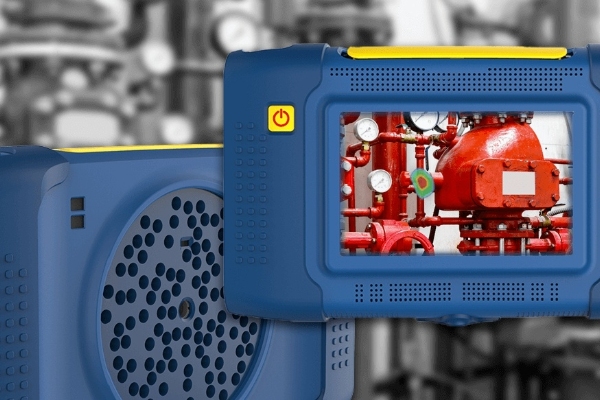
Conclusion.
Acoustic emission testing plays an important role in industry as a widely used non-destructive testing method.
It can monitor the integrity and defective condition of structures in real time, providing engineers with timely
support for safety assessment and maintenance decisions. Although there are some limitations of acoustic emission
testing, with the continuous development of technology and deeper research, we can expect its further improvement
and expansion in future applications.