In modern industry, non-destructive testing (NDT) techniques are widely utilized to ensure the quality and
safety of products. Eddy current testing (ET), as a common NDT method, has attracted much attention for
its high efficiency, sensitivity and accuracy. In this paper, we will discuss the principles and applications of
eddy current testing and its importance in the industrial field.
Introduction of Principle
Eddy current inspection is a technique for detecting internal defects in materials by utilizing eddy current
induction. Its principle is based on Ampere's law and Faraday's law of electromagnetic induction. When an
alternating current is passed through a coil, an alternating magnetic field is generated between the coil and
the material under test. If defects, such as cracks or holes, exist in the material under test, the alternating
magnetic field will result in the formation of eddy currents. By detecting the strength and distribution of
the eddy currents, we can determine the location and size of the defects in the material.
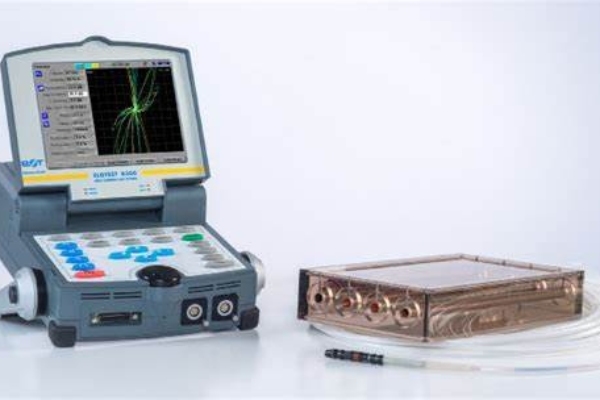
Fields of application
Eddy current inspection is widely used in different areas of industrial production. Below are some examples
of common applications:
Aerospace industry: In the manufacture of aircraft and spacecraft, eddy current inspection can be used to
detect defects in critical components such as engine blades, metal structures and welded joints. This helps
ensure the structural integrity and safety of the vehicle.
Automotive industry: In automotive manufacturing, eddy current inspection is used to detect defects in engine
components, wheel bearings and welding defects. This helps to improve the quality and reliability of automobiles.
Railroad industry: Eddy current inspection is used to detect surface cracks, rail joints and welds in railroad
tracks to ensure safe railroad operation.
Oil and gas industry: Eddy current inspection can be used to detect defects such as corrosion, cracks and
fatigue during pipeline and vessel manufacturing to prevent leaks and accidents.
Importance and advantages
The reasons why eddy current inspection is important and widely used in industry are as follows:
Efficiency: Eddy current inspection is a fast and efficient non-destructive testing method. Through the
reasonable arrangement of probes, it can be used to quickly inspect large areas of materials and improve
production efficiency.
High sensitivity: Eddy current inspection can detect tiny defects, such as micro-cracks and tiny holes,
and its sensitivity is higher than that of general visualization methods.
Non-destructive: Since eddy current inspection is a non-contact, non-destructive testing technique, it does
not cause any damage to the material under test and maintains the integrity of the material.
Can be automated: eddy current testing can be combined with computer systems to realize automation and
remote control, improving the accuracy and stability of testing.
In modern industry, non-destructive testing techniques are widely utilized to ensure product quality and safety.
Eddy current testing (ET), as a common NDT method, has attracted much attention for its high efficiency,
sensitivity and accuracy. In this paper, we will discuss the principles and applications of eddy current testing
and its importance in the industrial field.
Introduction of Principle
Eddy current inspection is a technique for detecting internal defects in materials by utilizing eddy current
induction. Its principle is based on Ampere's law and Faraday's law of electromagnetic induction. When an
alternating current is passed through a coil, an alternating magnetic field is generated between the coil
and the material under test. If defects, such as cracks or holes, exist in the material under test, the alternating
magnetic field will result in the formation of eddy currents. By detecting the strength and distribution of the
eddy currents, we can determine the location and size of the defects in the material.
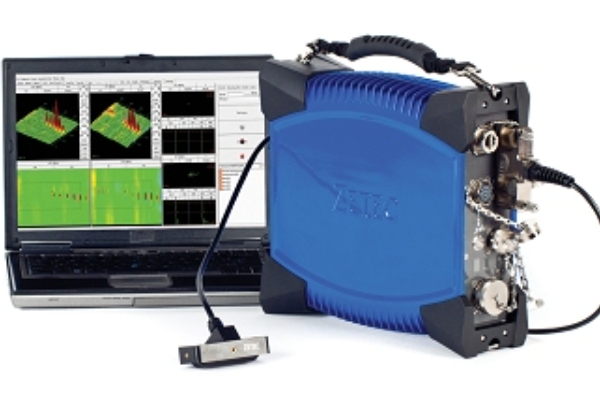
Conclusion
Nondestructive testing plays a vital role in modern industrial production, and eddy current testing, as one of the
methods, is characterized by high efficiency, sensitivity and accuracy. Its wide application in aerospace, automotive,
railroad, oil and gas industries makes it a key technology to ensure product quality and safety. In the future, with
the further development of technology, eddy current inspection is expected to play a role in more industrial fields
and provide more convenience and guarantee for production.