Non-destructive testing (NDT) is an important technology with a wide range of applications in engineering, manufacturing and restoration. Among them, visual testing (VT) is a simple but
effective method of directly observing and analyzing the surface of a material or component by the human eye to detect possible defects and damages. In this paper, we will discuss the principles,
benefits and applications of visual inspection in practice.
Principles and Methods of Visual Inspection
Visual inspection, as a non-destructive testing technique, is based on the human eye observing and judging the appearance characteristics of a material or component to detect possible defects,
cracks or other damage. This method does not rely on any instrumentation, but rather on the experience and skill of a professional. During visual inspection, operators use their eyes to scrutinize
areas of the object being inspected for clues to possible defects. They pay attention to the color, shape, texture and other visible features of the material's surface in order to identify potential
problems. Professionals also utilize auxiliary tools, such as magnifying glasses, projector lights and cameras, in order to more clearly observe and document the defects found.
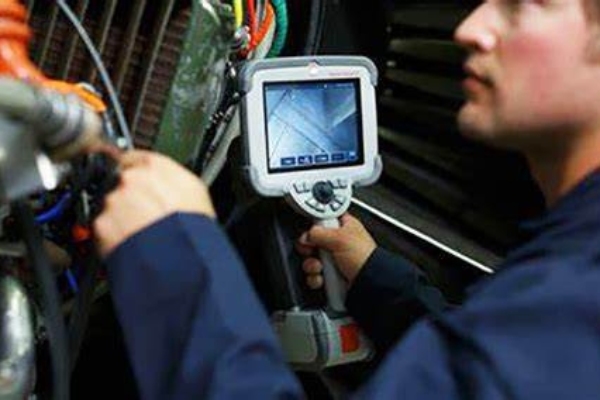
Advantages of Visual Inspection
Visual inspection offers several advantages that make it one of the most commonly used NDT methods in many industries:
Intuitive: Visual inspection is a method of directly observing and evaluating a material or component without the need for complex instrumentation. Professionals can see and feel possible
defects directly, leading to a better understanding of the nature of the problem.
Cost-effective: Visual inspection is less expensive than other advanced NDT techniques. It does not require expensive equipment and extensive training, which can help organizations save money
in the long run.
Real-time: Since visual inspection does not require any delay time or test preparation, it can be performed in real-time. This allows professionals to quickly identify and solve potential problems,
thus increasing productivity and production safety.
Application areas of visual inspection
Visual inspection is used in a wide range of different fields and industries, here are a few of the main application areas:
Aerospace: In aerospace engineering, visual inspection is used to assess aircraft surface defects, weld quality and other factors that may affect flight safety. Aerospace engineers and maintenance
personnel can use visual inspection methods to ensure that an aircraft meets safety standards prior to operation.
Construction and Civil Engineering: In the field of construction and civil engineering, visual inspection is used to assess the quality of construction materials and detect damage such as cracks,
corrosion or fatigue in concrete and metal structures. This helps to ensure the structural safety and long-term reliability of buildings.
Automotive Manufacturing and Repair: In the automotive manufacturing and repair industry, visual inspection is widely used to check the quality and integrity of components. For example,
on an automotive assembly line, workers use visual inspection methods to confirm the appearance and quality of each component to ensure the safety and performance of the final product.
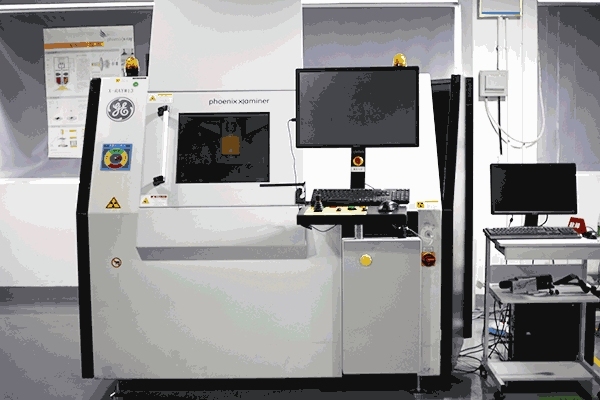
Conclusion
Despite its relative simplicity as a non-destructive testing method, visual inspection continues to play an important role in many industries. The intuitive and cost-effective nature of visual inspection makes it a reliable and widely used technique. Whether it is aerospace, construction and civil engineering, or automotive manufacturing and repair, visual inspection can help professionals identify problems in a timely manner, thus ensuring the quality and safety of products and projects.