Since its inception, the welding process has played an important role in human production and life, and covers almost all industrial sectors, such as construction, heavy industry, vehicles, ships, aerospace and so on. However, defects from inside and outside the weld usually lead to weld failures, such as reduced weld strength, poor weld sealing, and poor weld aesthetics. For this reason, two main types of testing methods are usually used to inspect the quality of welds, namely, non-destructive and destructive testing.
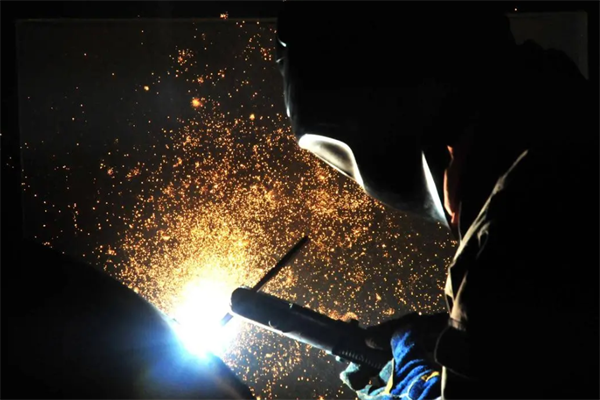
Weld strength testing tests include:
Tensile test
The tensile test is one of the most commonly used weld strength testing methods and is based on the principle of testing the strength of a welded joint by applying a tensile force. For the test, the welded joint is fixed on a testing machine and then a gradually increasing tensile force is applied until the welded joint breaks. The strength of the welded joint can be calculated from the maximum tensile force applied before fracture.
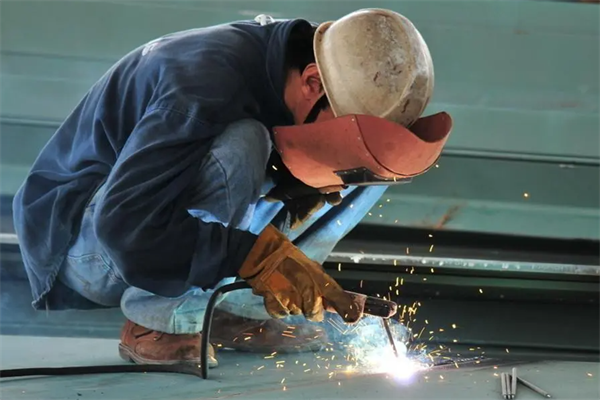
Shear Test
The shear test is another commonly used method of testing the strength of welded joints by applying a shear force. For the test, the welded joint is fixed to a testing machine and then a gradually increasing shear force is applied until the welded joint breaks. The strength of the welded joint can be calculated from the maximum shear force applied before fracture.
Hardness Test
The hardness test is an indirect method of testing the strength of a weld, based on the principle that the strength of a welded joint is deduced by measuring its hardness. During the test, a hardness tester is used to measure the welded joint, and the strength of the welded joint can be calculated from the measurement results.