Molybdenum , chemical symbol Mo, atomic number 42, is a transition metal element. Molybdenum is a silver-white metal, molybdenum atomic radius of 0.14nm, atomic volume of 235.5px/mol, coordination number of 8, the crystal is Az-type body-centered cubic crystal system, the space group is Oh9, so far it has not been found to have an isomerization transition. The lattice parameter of molybdenum at room temperature ranges from 0.31467 to 0.31475 nm and varies with the impurity content. Molybdenum has a very high melting point, ranking sixth among the monomers in nature, and is known as a refractory metal. The density of molybdenum is 10.23g/cm3, about half that of tungsten (tungsten density 19.36g/cm3). Molybdenum has a low coefficient of thermal expansion; molybdenum has a high thermal conductivity. Molybdenum resistivity is low: 5.17×10-10Ω-cm at 0 ℃; 24.6×10-10Ω-cm at 800 ℃; 72×10-10Ω-cm at 2400 ℃. molybdenum is a paramagnet, molybdenum's specific heat at 25 ℃ is 242.8J/(kg-K). Molybdenum's hardness is large, the Mohs hardness is 5~5.5. Molybdenum at the boiling point of the heat of evaporation is 594kJ/mol; the heat of melting is 27.6±2.9kJ/mol; the heat of sublimation at 25℃ is 659kJ/mol.
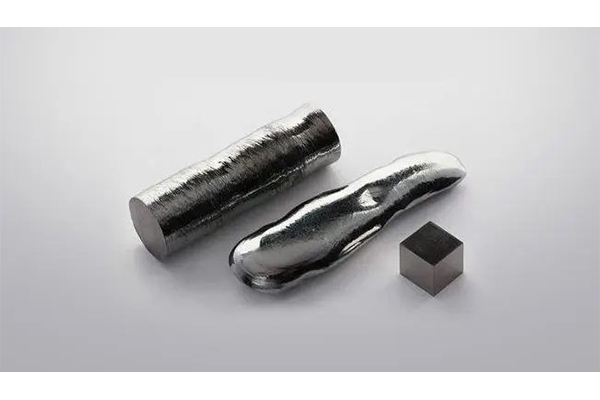
Molybdenum (Mo)
1、Molybdenum has solid solution strengthening effect on ferrite, improving the strength and hardness of steel.
2、Improve the heat resistance and high temperature strength of steel.
3、Anti-hydrogen erosion effect.
4, reduce the critical cooling rate of steel, improve the hardenability of steel.
Disadvantages: The main adverse effect of molybdenum is its tendency to graphitize low-alloy molybdenum steels.
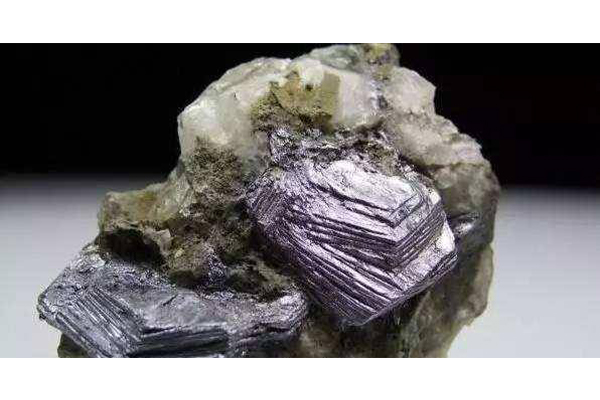
Molybdenum is used above all in the iron and steel industry, which accounts for around 80% of the total consumption of molybdenum, followed by the chemical industry with around 10%. In addition, molybdenum is also used in the fields of electrical and electronic technology, medicine and agriculture, which account for around 10 percent of total consumption.
Molybdenum is most consumed in the steel sector, where it is mainly used in the production of alloy steels (approx. 43% of total molybdenum consumption in steel), stainless steels (approx. 23%), tool steels and high-speed steels (approx. 8%), and cast irons and rolls (approx. 6%). Most of the molybdenum is used directly in steelmaking or cast iron after being briquetted as industrial molybdenum oxide, while a small proportion is first smelted into ferromolybdenum and then used in steelmaking. Molybdenum as an alloying element in steel has the following advantages: it increases the strength and toughness of the steel; it improves the corrosion resistance of the steel in acid and alkaline solutions and liquid metals; it increases the wear resistance of the steel; and it improves the hardenability, weldability, and heat resistance of the steel. For example, stainless steels containing 4-5% molybdenum are often used in places where erosion and corrosion are more severe, such as marine equipment and chemical equipment.
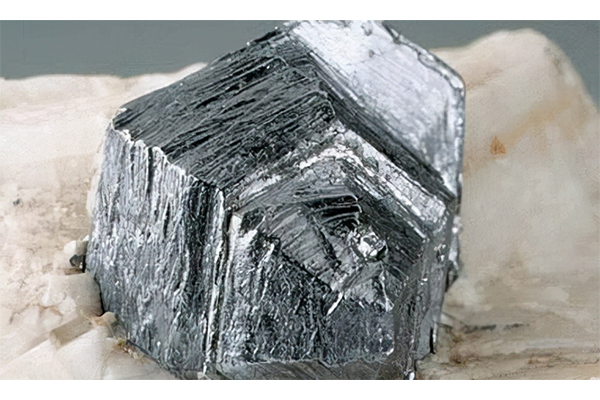
Molybdenum-copper alloys applied to the aerospace field take molybdenum as the base to add other elements (such as titanium, zirconium, hafnium, tungsten and rare earth elements, etc.) to form a non-ferrous alloy, these alloying elements not only play a role in solid solution strengthening of molybdenum alloys and maintaining low-temperature plasticity, but also form a stable, diffusely distributed carbide phase to increase the strength and recrystallization temperature of the alloy. Molybdenum-based alloys are used in high heat generating elements, extruded abrasives, glass melting furnace electrodes, spray coatings, metal working tools, and spacecraft components because of their good strength, mechanical stability, and high ductility.