This paper discusses infrared detection technology (ET) in nondestructive testing, which has a wide range of applications in industry and research. We will explore the principles and advantages of
infrared inspection and present some relevant case studies to support our arguments
Non-destructive testing (NDT) techniques play an important role in modern industrial production and scientific research. They can help us to detect hidden defects in materials and structures,
thus avoiding problems that could lead to serious consequences. In this paper, we will focus on a technique that is widely used in NDT inspection: infrared inspection.
Principles of Infrared Inspection
Infrared testing (ET) detects hidden defects by utilizing the thermal radiation emitted by a material or structure, which is located in the long-wave infrared region of the electromagnetic spectrum.
When a material or structure has a defect, its absorption and emission coefficients for visible and infrared radiation change. With equipment such as infrared cameras, we can measure and
display this change to detect the presence of defects.
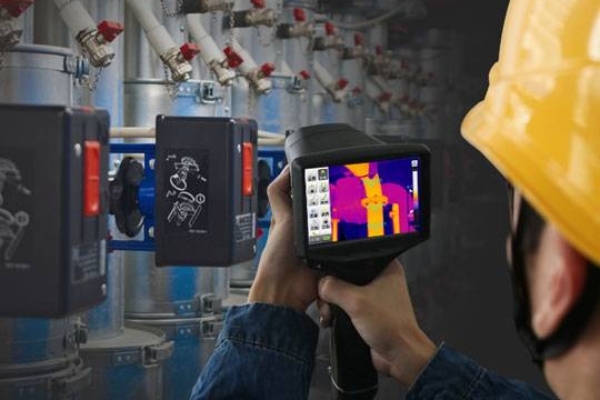
Advantages of infrared testing
Compared with traditional non-destructive testing techniques, infrared testing has the following advantages:
Non-contact detection: Infrared inspection uses infrared cameras and other equipment for observation without direct contact with the object being inspected, reducing the interference of the
testing process with the object being inspected.
All-day performance: Since infrared inspection is achieved by measuring thermal radiation, it can be performed at different times of the day and under different environmental conditions,
including dark nights and harsh weather conditions.
Wide applicability: Infrared detection is not limited by the type of material and can be applied to a wide range of materials such as metals, composites and ceramics.
High sensitivity: Infrared inspection technology is able to detect small temperature changes, thus discovering hidden defects, and even tiny hot spots can be effectively detected.
Application Cases of Infrared Inspection
Case Study 1: Aircraft Structure Inspection
A study conducted infrared testing for non-destructive testing of aircraft structures. The team used an infrared camera to scan the aircraft's shell and found a number of tiny temperature
anomalies. Further analysis revealed that the anomalies were caused by structural defects that were difficult to detect through other inspection methods. Infrared inspection technology
helped engineers find and fix these potential problems in time, improving the safety and reliability of the airplane.
Case Study 2: Oil Pipeline Leak Detection
Leaks are a serious safety hazard in the oil industry. A study used infrared detection technology to monitor an oil pipeline and found a tiny hot spot. Through further analysis, engineers
determined that it was caused by a pipeline leak. The leak was repaired in a timely manner, preventing an unforeseen event that could have led to environmental damage and injuries.
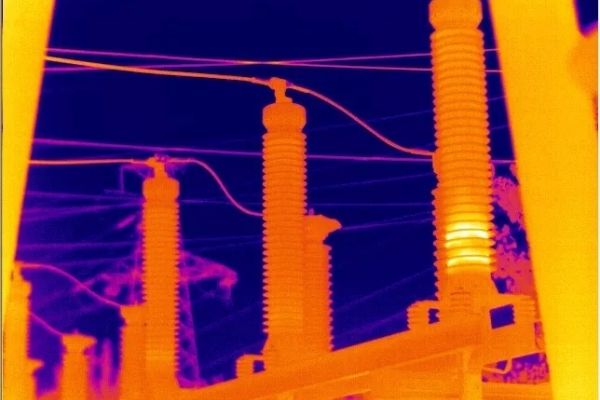
Conclusion
Infrared inspection technology has important applications in the field of nondestructive testing. Its non-contact, all-day performance, wide applicability and high sensitivity make it an indispensable tool in industry and scientific research. Through the introduction of the principles, advantages and application cases of infrared detection in this paper, we are convinced that infrared detection technology will continue to play an important role in providing more accurate and efficient solutions for nondestructive detection work in various industries.