Sulfur (S)
1, sulfur in steel to FeS-Fe co-crystals exist in the grain boundaries of steel, reducing the mechanical properties of steel, excellent steel sulfur content should generally be limited to less than 0.04%.
2, in mechanical manufacturing, sometimes in order to improve the cutting performance of certain steels, artificially increase the sulfur content, in order to form sulfides, to interrupt the role of matrix continuity.
Disadvantage: the increase in sulfur content, increase the tendency of casting thermal cracking.
First, the role of carbon in metal materials carbon is a common element, it has an important role in metal materials. The carbon content in the metal is usually between 0.1% and 2%, and even if there is only a small change, it will have a significant impact on the performance of the metal material. The effect of carbon on metals depends on its form and content. Carbon can be present in metals in different forms, such as twinning, spheroidization, carbides, etc.
The main role of carbon in steel is to increase hardness and strength. By controlling the amount of carbon in steel, the hardness and strength of the steel can be regulated and it can be made to have better cutting and wear properties. However, excess carbon can make steel brittle and prone to fracture. Therefore, for different application scenarios, steels with different carbon contents need to be selected to meet the performance requirements.
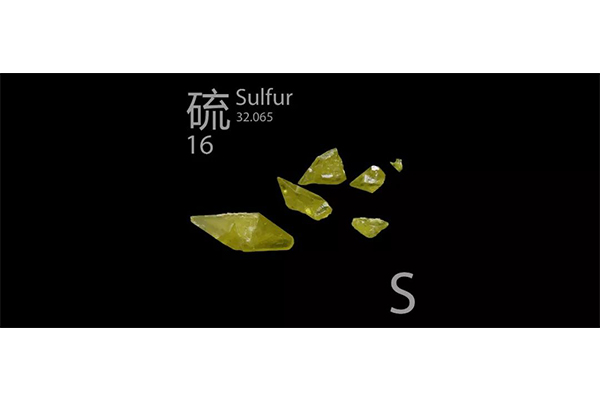
Second, the role of sulfur in metal materials sulfur is a common impurity element, which often exists in the form of sulfides in metal materials. Although the amount of sulfur is usually low, it has a significant effect on the properties of metallic materials. The main effect of sulfur is to make metals brittle and susceptible to thermal cracking. In addition, sulfur affects the cold working properties and forming properties of metals.
Sulfur content needs to be controlled during the metal manufacturing process. If the sulfur content is too high, different desulfurization methods, such as vacuum melting and electroslag remelting, can be used to reduce the sulfur content and improve the properties of metal materials.
Third, how to detect the carbon and sulfur content of metal materials to understand the carbon and sulfur content in the metal is very important to ensure the performance of metal materials. In modern manufacturing, the common method is to use analytical instruments for detection.
For the detection of carbon content, you can use carbon and sulfur analyzers or spectrum analyzers. These instruments can quickly and accurately detect the carbon content in metals and adjust it according to the needs.
In addition to this, sulfur in metals affects their weldability and casting properties. The presence of sulfur increases the brittleness of metals, causing them to be prone to defects such as cracking or fracture during processing, which affects the mechanical properties and life of parts. In iron and steel smelting, in order to reduce the content of sulfur, often take the method of adding roasted lime, silicate and other reducing agents, so that sulfur is reduced to gaseous sulfide, discharged with the slag.
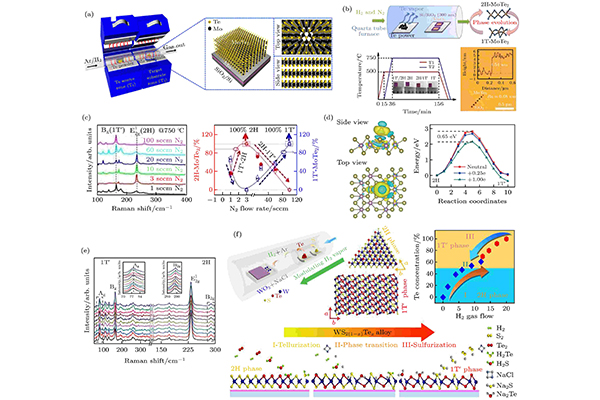
In addition, carbon and sulphur also have an effect on the surface of metallic materials during processing and use. For example, the higher content of carbon in steel will make the surface hardening, improve wear resistance and cutting, while the lower content will make the surface softer and easy to cold deformation; sulfur will reduce the surface finish of the metal, resulting in a larger coefficient of friction.
In summary, carbon and sulfur in metal materials are common impurity elements, and their presence will have different degrees of influence on the properties of metals. Therefore, in the production and use of metal materials, it is necessary to strictly control and test their composition and content to ensure that the quality and performance of the products meet the requirements. At the same time, for different application scenarios, the performance and adaptability of metals can be adjusted by controlling the content and ratio of carbon and sulfur to improve their benefits and value in industrial production.
The role of sulfur in steel is to reduce the ductility and toughness of steel, impair the corrosion resistance of steel, and have a negative impact on welding.
Steel generally refers to iron-carbon alloys.
Iron-carbon alloys, are binary alloys composed of iron and carbon.
Iron-based materials in the most widely used category, carbon steel and cast iron, is an industrial iron-carbon alloy materials.
Iron and steel materials for a wide range of reasons, first of all, lies in the composition of the available span, from nearly carbon-free industrial pure iron to about 4% of the carbon content of cast iron, in this range of alloy phase structure and microstructure of the alloys have undergone great changes, in addition, also lies in the use of a variety of thermal processing technology, especially metal heat treatment technology, significantly change the organization and properties of a composition of alloys.
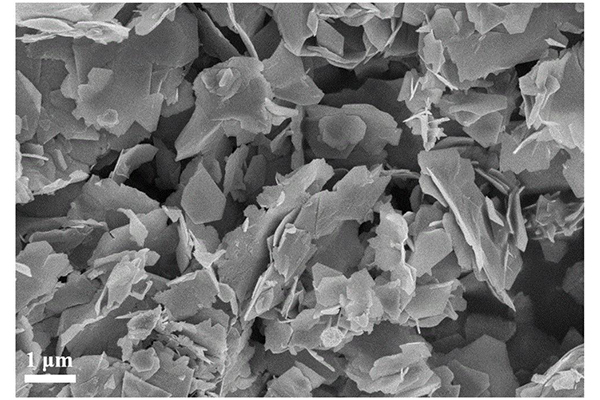