Structural health inspection technology is an important means of routine 'physical examination' and 'health' monitoring of buildings or structures that has emerged in recent years, and the main method is to utilize intelligent sensing instruments for real-time monitoring, dynamic management and trend research and judgment of the structure of buildings or structures.
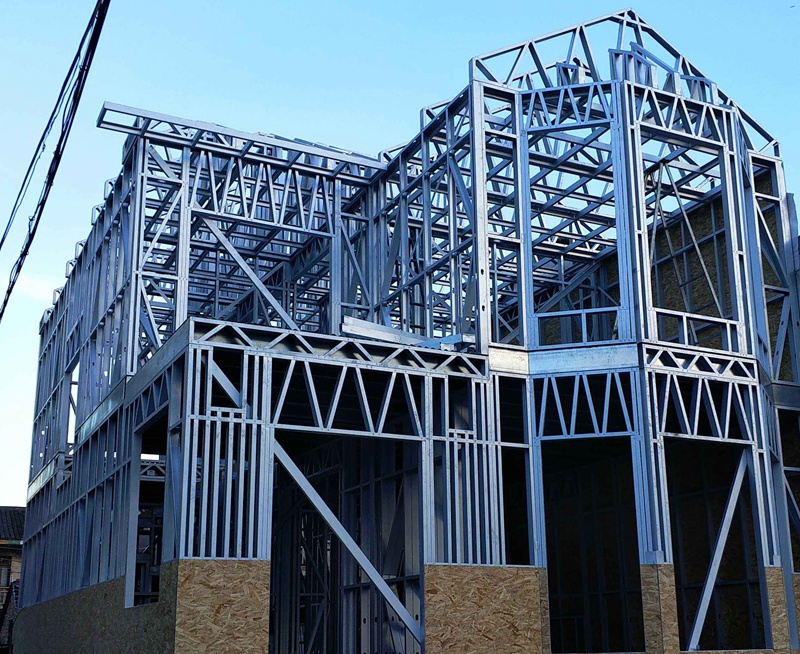
By pre-embedding or attaching various types of sensors inside or on the surface of the monitored object to form a monitoring network, real-time sensing of important information about the behavioral response of the building structure to its own service status, external environmental erosion, extreme loading, and peripheral disturbance invasion, in order to make intelligent assessment and decision-making on its damage, performance degradation, operational efficiency and other health conditions, and provide scientific basis for the safe use, maintenance and life span prediction of the building structure. It provides a scientific basis for the safe use, maintenance and maintenance of building structures and the prediction of their lifespan.
Structure Health Monitoring (SHM) is an automated system of condition monitoring, feature identification and condition assessment for the long-term service safety of engineering structures, which provides decision support for the management and maintenance of structures. Structure Health Monitoring transforms the traditional offline, static and asynchronous manual inspection method into an online, dynamic and synchronized modern monitoring technology.
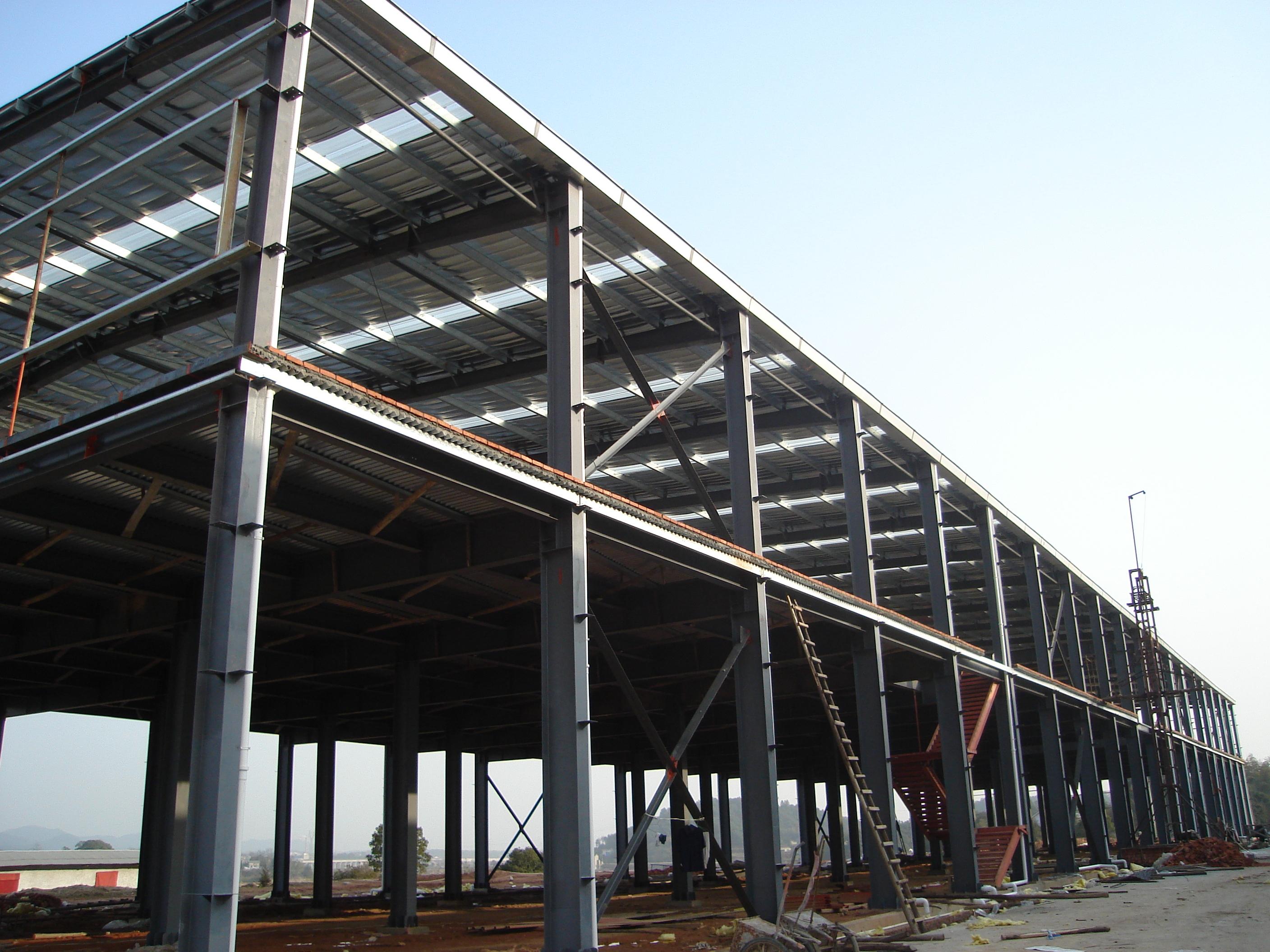
In short, it is a means to monitor the safety status of a building
A complete structural health monitoring system usually consists of five parts, i.e., sensor subsystem, data acquisition subsystem, data transmission subsystem, data storage and management subsystem, and structural warning and assessment subsystem.
1. Sensor subsystem. The sensor subsystem is mainly composed of sensing elements that can sense four types of physical quantities, namely, environment and loading, structural response, structural geometric deformation, and structural durability, and is optimally deployed according to the principles of structural mechanics, so as to realize a comprehensive perception of the overall and local performance of the structure.
2. Data acquisition subsystem. The data acquisition subsystem consists of hardware acquisition equipment and software modules, which collects physical quantities to be sensed in real-time, timed, triggered or mixed modes, and requires simultaneous control, synchronous acquisition and high-speed demodulation of various types of sensor signals to achieve high-quality acquisition of monitoring data.
3. Data transmission subsystem. The data transmission subsystem includes transmission cables, switches, signal transceivers and amplifiers, etc., which are networked by bus, ring, star, tree or hybrid structure, and the collected data are transmitted to the data storage and management subsystem by wired or wireless means.
4. Data storage and management subsystem. The data storage and management subsystem can be composed of the central database, data management software and hardware, etc., providing functions of storing, querying, calling and simple statistical analysis of the monitoring data and the structure's own information.
5. Structure early warning and assessment subsystem. The structural early warning and assessment subsystem is mainly composed of high-performance computer and professional analysis software, and its function is to carry out mechanical analysis on the pre-processed data, including model correction, modal identification, damage diagnosis, condition assessment, life prediction, maintenance decision-making and so on.